Revolutionising Mineral Separation using Additive Manufacturing
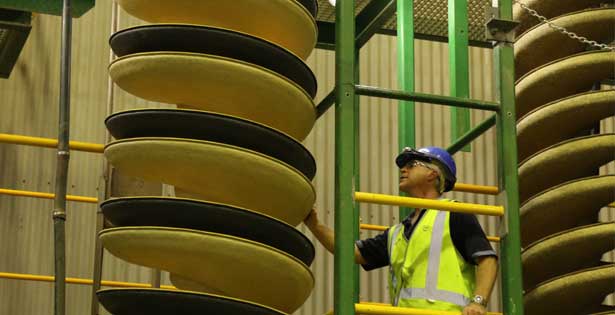
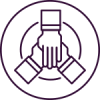
Industry partner
Mineral Technologies
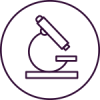
Research organisation
University of Technology Sydney
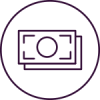
Manufacturing Investment
$9,309,045
($1,800,000 IMCRC)
for 2018–2022
3D printing to create precision-engineered mining equipment
Challenge
Gravity concentrators (also known as spirals) are cumbersome and costly to manufacture, often exposing operators to chemicals and other hazards. Over the last 15 years, alternative technologies such as Resin Transfer Moulding and Injection Moulding have been explored and consistently found to be unviable for application due to the number of different spiral models needed in the field, each requiring numerous moulds.
Proposed Solution
Mineral Technologies (MT) has partnered with the University of Technology Sydney (UTS) to research solutions that will revolutionise how composite polymers are used to manufacture precision-engineered mineral separation and mining equipment.
In the first instance, the project will investigate using complex and efficient geometries to redesign the helically shaped gravity concentrator, in a way suited to an existing 3D printing technology. A product specific 3D printing machine will then be designed and prototyped to optimise the manufacturing process of the gravity concentrator. Fitted with Internet of Things (IoT) sensors the new concentrators will provide feedback about the product performance and give insight into equivalent wear and structural characteristics for specific minerals and ore concentrations.
Throughout the project, MT will collaborate with other Australian SMEs to develop and test the new manufacturing method and various selected materials to support the rapid 3D printing operations.