Advanced engineered surfaces for hydrometallurgy ball valves
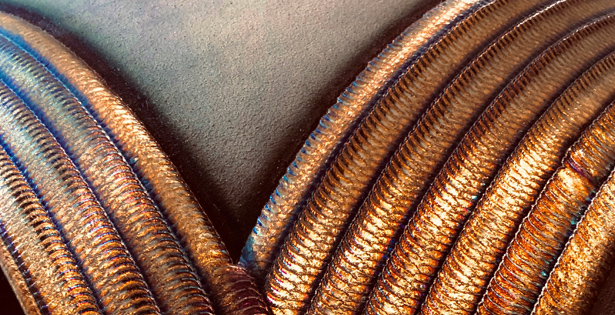
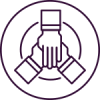
Industry partner
Callidus Welding Solutions
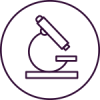
Research organisation
Deakin University
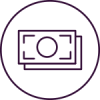
Manufacturing investment
$692,787
($99,922 IMCRC)
for 2021
Controlling and maintaining safety in hydrometallurgy production of critical minerals
Challenge
Seated ball valves are critical infrastructure components used for flow control in hydrometallurgy reactors. They are made out of high-performance alloys to withstand the hydrometallurgical severe service conditions consisting of high temperature, high pressure and corrosive medium. Ceramic oxide coatings are conventionally applied on top of internal component surfaces for protection and to lengthen the component’s lifetime in service. Yet, the coatings inherently contain micron-scale interconnected pores and only form a mechanical bond to the substrate. Consequently, the failure of these coatings is commonly due to under-coating corrosion and ultimately spallation of the coating which compromises the performance, safety and efficiency of the entire hydrometallurgy operation.
Proposed Solution
In partnership with Deakin University, Callidus Welding Solutions (CWS) has set out to develop a “fused” coating system that lifts the surface performance on dominant alloys in hydrometallurgical reactors.
Metallurgy experts from Deakin’s Institute for Frontier Materials (IFM) have innovated a surface modification that extends the life of titanium components used in the hydrometallurgy industry. As part of the 12-month project, the technology will be developed by CWS to apply the novel surface modification to seated ball valves and test how it performs in service.
Once successfully tested, CWS aims to commercialise and pass on the benefits – a product with improved surface performance and thus longer operation cycles – to their customers.
As the project represents an overall step change in the surface performance, CWS plans to apply the new concept to the next generation of coatings.